January 2022
Service pits in quick lube stations and other vehicle maintenance facilities help increase efficiency and productivity by making it easier to get the job done. However, this convenience comes at a price, as they present a major fall hazard to busy employees and wandering customers. OSHA requires that a protective covering or guard must be used over service pits to eliminate these risks. However, many shops still choose to ignore these dangers and the guidelines, hoping to save a few bucks.
In the long term, the opposite often holds true. The costs are much greater, if not immeasurable. The more time that passes with service pits being unprotected, the more likely someone will fall in, get injured, or worse. Not to mention the tremendous resource drain this poses as a result. These dangers can be reduced and eliminated with the proper use of a safety system specifically designed to cover these openings when not in use.
BayNets are a popular choice to avoid these dangers. These are netting systems that are custom-made to fit precisely over the opening. They are secured with fasteners that allow the net to freely slide open and closed as needed – much like a shower curtain. The net itself is composed of strong material that is engineered to catch people. BayNets are durable, and easy to operate and maintain.
By far, the most important reason to install a service pit safety system such as BayNets is to prevent accidents that could result in injuries and possible loss of life. Once an incident happens, there is much involved, including:
- Lawsuits
- Fines
- OSHA violations
- Worker’s Compensation claims
- Mountains of paperwork and time-consuming interviews
- Negative press for the company
- Decline in business
Keep in mind that when an accident happens, the shop gets shut down. This leads to further issues such as immediate and long-term loss of business and revenue. Retail customers will often head to a competitor and may never return. Employees get disheartened as well. Just imagine it from their point of view: a coworker was hurt as a result of negligence, leaving them to wonder, “What type of company am I working for? Could I be next?” Their paychecks suffer as well. We’ve heard plenty of stories where good employees have left after avoidable accidents happened. Now management must seek and train their replacements.
Conversely, when a proper safety solution is utilized, many of the potential negatives turn into positives. By keeping people safe, you are sending a strong message that management cares about their employees. They are not working in a fearful environment. Instead, they are in a safe shop. This means increased morale and productivity with lower employee turnover. This equates to better profitability for the company.
Unfortunately, we often get calls after it’s too late. An accident has occurred and now the customer must have protection in place ASAP to prevent future ones and comply with regulations. Essentially, they are trying to lock the barn doors long after the horses have bolted. In these cases, delivery requirements are often extremely tight, which means rush fees may be charged. While they finally wind up with a safer workplace, the damage is done. All of it was completely avoidable.
Are BayNets the only solution?
Other types of systems are available to secure service pits. These include webbing systems and metal grates. It’s been reported that some webbing systems have a tendency to jam, and metal grates can be heavy, difficult to operate, and become unusable if bent. Other nets are available as well, such as fishnets. But keep in mind, these were not designed to catch humans. In essence, you’ll have merely the illusion of safety, like an empty fire extinguisher. You don’t want to learn that lesson after someone falls through.
When considering which solution is best for your shop, we encourage you to research all of the benefits and potential drawbacks. It’s not just about cost either. In fact, it’s easy to spend too much on an over-engineered system that is more problematic over time due to unnecessary complexity.
In the end, you’ll want to be sure to have a system that is worth the investment in the long run. One that functions properly and consistently, and does what it’s intended to do: protect people from injury and help keep your business up and running efficiently and safely. Download information Sell Sheet
About InCord
InCord manufactures custom safety netting solutions and lifting and rigging products for a range of industries. Our woman-owned Colchester, CT manufacturing plant is an ISO-9001 certified facility, housing a team ready to design and fabricate a unique netting solution to fit your needs. InCord was founded in 1995 and is a Connecticut Top Workplace. To discuss an application, request a quote, or obtain technical guidance, please call us at (860) 537-1414, submit a request here, or email us at netting@incord.com.
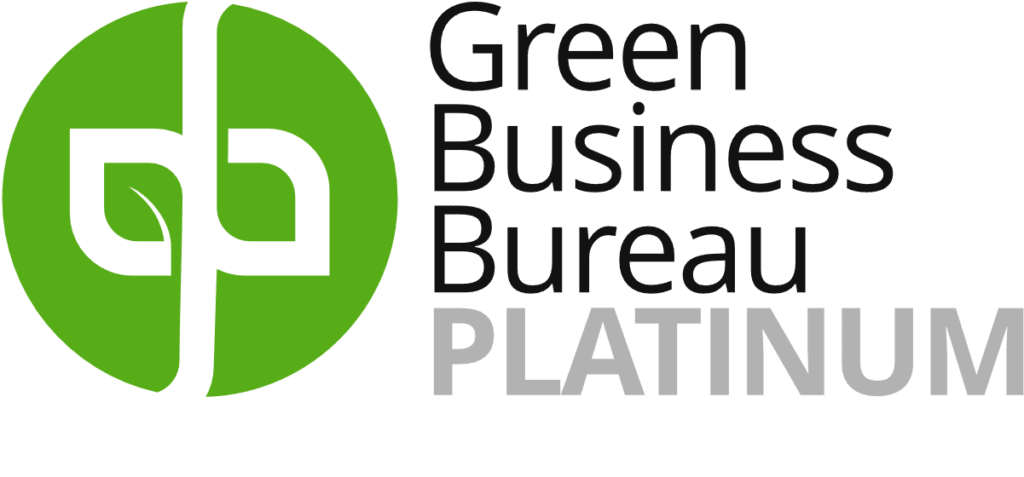
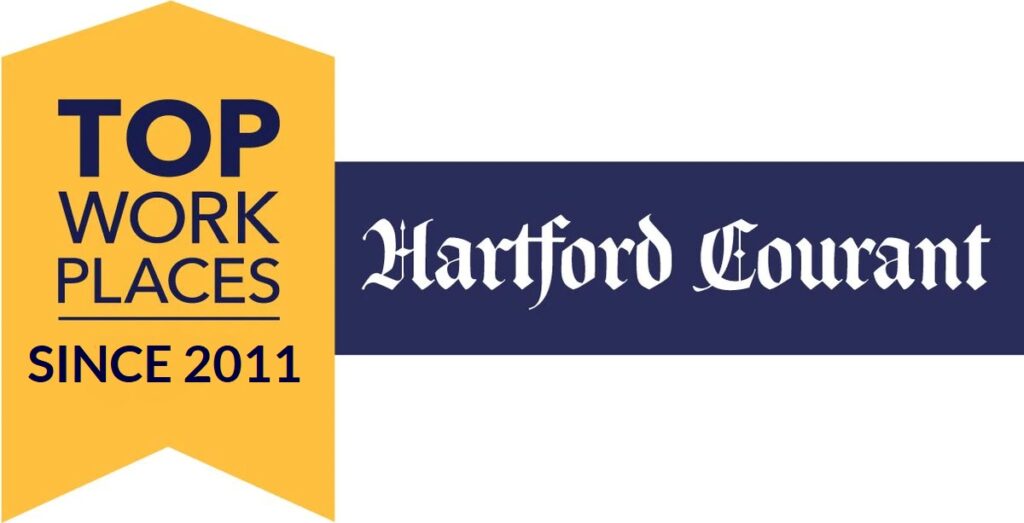
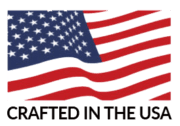