Warehouse Rack Safety
Workplace safety is an ever-evolving topic, one under constant pressure to meet the shifting needs of employees, employers, regulators, and customers alike. All employees are due the right of a safe and healthy workplace yet putting a zero-accident program in place is still not a universal, standardized process. Our customers often ask for guidance on where to turn for regulatory requirements, safety best practices, and specific safety solutions, especially concerning warehouse racking systems and their surrounding spaces. In the spirit of answering this question for a wider audience, we’ve prepared this article outlining a comprehensive approach to Warehouse Rack Safety, starting with quantifying the need for continuous safety improvement in our industry and ending with very specific safety suggestions that you can put into practice right away.
The Case for Warehouse Safety
The United States has one of the safest employment landscapes in the world, thanks to the combined efforts of invested employers, diligent regulators, and emphatic worker protection groups. Still, accidents do happen, and as a result, safety systems must continue to improve. To get a sense for current domestic workplace safety levels, consider the following data:
- According to the Census of Fatal Occupational Injuries 2020 Summary, released by the US Bureau of Labor Statistics (BLS), there were 4,764 fatal work injuries in the US in 2020.
- Workers in material moving occupations made up 218 of these fatal accidents in 2020, or about 5%.
- According to a separate BLS report on Employer-Reported Workplace Injuries and Illnesses 2020, employers reported 2.7 million non-fatal workplace injuries and illnesses.
- Of the injury and illness incidents that resulted in days away from work, the category of employees “Laborers and Freight, Stack and Material Movers, Hand” saw the fourth-highest incident rate - approximately 300 cases per 10,000 full-time employees. This is only lower than Nursing Assistant, Licensed Medical Practitioner, and Registered Nurse categories (a sobering fact brought about mainly by the COVID-19 pandemic). “Stock and Order Fillers” were seventh on the list at approximately 180 cases per 10,000 full-time employees.
- Injury and illness incident rates for all employees in the Transportation and Warehousing sector was 4.0 in 2020, which translates to 4 cases per 100 full-time employees. This measurement is useful in comparing the relative safety of various industries. Consider against select other 2020 values:
- Overall Private Industry Average = 2.7
- Construction Industry = 2.5
- Educational Services = 1.1
- Health Care = 5.5
- Manufacturing = 3.1
- Accidents in warehouse and distribution spaces come in a variety of forms, from death by forklift overturning on one end of the severity scale (estimated by this report as 42% of all fatal forklift accidents), and lost-time slip/trip/fall/overexertion/bodily reaction injuries on the other end (estimated by a separate report as 84% of all nonfatal lost-time injuries).
- Liberty Mutual Insurance Company estimates that non-fatal accidents in the transportation and warehousing industry cost $84.04 million per week, as a combined total of medical, lost time, insurance, worker’s compensation, and associated expenses.
As we can see, the warehouse industry does statistically trend towards the ‘less safe than average’ end of the spectrum, consisting of more physical, laborious, vehicular, and mechanized hazards than others. Within the subset of injuries found in warehouse and distribution spaces, a portion of these have to do specifically with racking systems, and the potential hazards created by the materials stored within those systems. Falling objects, racking collapse due to forklift strikes, failure due to poor maintenance, and similar scenarios present hazards to warehouse employees that we would like to address in the rest of this article. To start, let’s take a look at the baseline regulatory requirements involved in installing and operating warehouse racking systems.
Regulatory Requirements for Warehouse Racking
The regulatory environment surrounding warehouse racking is an obscure one, so we’d like to outline what requirements govern the installation and use of racking systems. Many material handling articles will cite OSHA standards (or lack thereof) for warehouse racking, but that is far from the complete picture.
OSHA does not strictly regulate warehouse racking design, installation, or use details. Instead, OSHA’s concern is at a higher level, imploring businesses to provide safe work environments overall, leaving the details to other bodies. This leads us to a question: what other bodies are involved? Let’s list them all below:
- OSHA – regulates general safety in warehouse (and all other) businesses, as follows:
- General Duty Clause – applicable to all industries and businesses, this clause states that all employers shall provide employment free from recognized hazards
- Section 1910.176(a) – states that sufficient safe clearances are provided in material handling and storage schemes where mechanical equipment is in use, with aisles appropriately marked, clear and free of hazards
- Section 1910.176(b) – simply states that the storage of materials shall not create a hazard, including multi-tier storage schemes which must be stable and secure
- Section 1910.159(c)(10) – sets a clearance requirement between fire sprinkler heads materials below 18 inches minimum (such as in the case of materials on racks extended up near building fire sprinklers in the ceiling)
- ANSI (American National Standards Institute) – a private non-profit organization that provides standards for the design, testing, and utilization of manufactured products, with several standards written specifically for industrial storage racks, such as:
- 1-2012 – covers hot-formed and cold-rolled steel channel rack systems
- 3-2016 – covers cantilevered steel rack systems
- 2-2017 – covers welded wire rack decking
- State Building Code – warehouse racking presents a unique combination of risk factors, functioning as both industrial equipment and as fixed building elements. For this reason, building code gets involved in regulating racking systems. Building codes vary from state to state, either having a state-specific version developed, or recognizing the International Building Code (IBC). At a minimum, state building codes are concerned with details such as proper structural anchorage, layouts that do not present emergency exiting problems, proper occupancy and exiting capacity, and ADA (American Disabilities Act) compliance, where applicable.
- State Fire Code – racking systems are a known fire hazard, and have particular requirements and limitations around the material types, density, and height found within them targeted at reducing this fire hazard. Most states will reference requirements issued by the National Fire Protection Association (NFPA), and some states will add their own requirements as well. Fire elements that these codes evaluate include sprinkler design, airflow between material units, separation of incompatible materials that can lead to fire ignition, and arrangement of the warehouse for proper emergency access in the case of a fire. Multiple NFPA standards are involved, such as:
- NFPA 230 – covers standards for fire protection of bulk stored materials
- NFPA 231 – covers standards for general storage
- NFPA 231C – covers standards for the rack storage of bulk materials
- Local Codes – your specific city, town, county, or region may also have local codes and ordinances that apply to warehouse racking systems. Check with your local building and fire departments to confirm if any additional requirements apply to your project or space. These requirements may govern both initial installation as well as ongoing operations, as in the example of a local fire department requiring annual fire inspection walk-throughs.
- Industry-Specific Guidelines – your particular industry may have unique storage requirements or guidelines written to avoid potential issues associated with the specific materials you’re storing. For example in the agricultural industry, warehouse requirements for fertilizers cover heightened safety measures against airborne particulates, temperature management, and spill containment. Check with trade associations, academic centers, and industry consultants for relevant guidelines.
- Insurance Carrier Requirements – commercial insurance carriers often have their own stipulations for warehouse systems, needed to maintain insurance coverage. Check with your insurance agent to obtain any of their specific needs, which usually include material volume, fire sprinkler, and inventory valuation criteria matching your selected insurance policy.
- Manufacturer Requirements – last but not least, all warehouse racking manufacturers will have their own job-specific installation, operation, and maintenance requirements. Not only are these important for business owners to receive and thoroughly review upon installation, but they also serve as ongoing guidance resources for employee training, third-party audits, and regulatory inspections.
Top Warehouse Rack Safety Hazards
For the sake of discussion, we’d like to break apart the risks experienced in warehouse spaces into two separate categories:
Active Risks: These risks are associated with the movement of forklifts, materials, and traffic in a distribution space. These risks can be more or less probable of turning into accidents as traffic and safety precautions change throughout the day. Active risks can be generally avoided if all employees share high awareness, diligent training, and a sense of responsibility for each other’s safety.
Notable Active Risks include:
- Personnel struck by forklift
- Rack frame struck by forklift
- Forklift overturning
- Wet / dirty floor
- Material fall caused by forklift
- Complacency
Passive Risks: These risks are present at all times in a warehouse, associated with the static loads of heavy stacked materials on rack structures in a confined space. Passive risks are generally present regardless of ongoing activity. Passive risks can be most often avoided through proper attention and care during installation and throughout the life of the racks, coupled with consistent inspection and evaluation.
Notable Passive Risks include:
- Rack failure or material fall due to earthquake
- Inadequate installation
- Insufficient maintenance
- Load shifting/settling
- Material fire
- Obscure evacuation path
Prioritizing Warehouse Safety
From reading all of the above information, you might have the impression that warehouses and distribution centers are inherently risky workplaces. Yes, they can be, however there are plenty of steps that employers and employees alike can take to assure that their warehouse spaces are trustfully and reliably safe.
- Training: When it comes to safety, we like to use the phrase ‘awareness is the first step’. Employers must be aware of the inherent risks associated with storing materials in high density warehouse rack arrays, and employees must be aware of the risks associated with working around these storage systems. Once made aware of the risks on hand, the next step is to frequently review, refresh, and rehearse safety procedures and scenarios, so that safe reactions and decisions become second nature. We suggest a full suite of training for your staff, starting with daily ‘heads-up’ reminders, weekly safety re-caps, and frequent larger retraining and certification as needed, covering topics such as:
- Forklift Operation (for fork truck operators)
- Forklift and Equipment Awareness (for employees working adjacent to material handling equipment)
- Rack Loading and Unloading (specific to your racking design as well as your material and packaging sizes, weights, and shapes)
- Emergency Communication, Evacuation Paths, Procedures, and Assembly Locations
- Spill Response
- Hazard Communication
- General Housekeeping
- Rack Inspections: Looming failures within pallet rack structures often announce themselves ahead of time, if only we look. Referring back to our phrase ‘awareness is the first step’, a great way to gain this crucial insight into the health and resilience of a racking system is to perform frequent, thorough inspections. Establish an inspection program that fully covers two objectives:
- Proper evaluation, identification and rating of hazards in the racking system, its structure, and its surroundings
- Immediate procedures for placing hazardous rack segments out of service, obtaining repairs and remediation, and communicating the hazard to all impacted parties
- Rack inspection programs should look for any and all indications of potential failures or hazardous scenarios such as:
- Bent or deflected columns
- Twisted foot pads or columns
- Areas of high wear and tear
- Areas missing paint or that have rust/corrosion
- Crossbars, supports, or stabilizing members not fully connected (IE loose bolts or clips)
- Visible tilt or out-of-alignment
- Foot anchors damaged or broken off
- Incorrect pallet or container sizes being stored
- Odd sounds - clanking, rattling, hollow or ringing noises
- Damaged or missing protective barriers and guards
- Fading / worn traffic lane markings
- Poor lighting and visibility
- Dirty or damaged traffic mirrors
- Presence and legibility of capacity nameplates, warning signs, and other manufacturer markings
- Unapproved modifications to rack structures
- Protective Equipment; Keeping safe around warehouse racking can be greatly enhanced through the use of protective equipment and gear.
- PPE (Personal Protective Equipment) – employees should wear properly fitted gloves, hard hats, high-visibility safety vests, and safety toe shoes in warehouse environments. Additional PPE requirements may be necessary in some environments such as full-length pants and shirts, safety glasses, back braces, hearing protection, and/or on-body blinking lighting.
- Safety Netting – protecting employees from falling materials, safety netting can be installed vertically or horizontally, below conveyors, above sorting lines, on the sides, rear or front of pallet rack. InCord safety netting is available in a variety of mesh sizes and strengths from 500 ft-lb light load capacity netting for small package protection to 6,000 ft-lb heavy duty mesh safety netting for full pallet protection. Optional debris liners can be added to contain small materials that may shake loose under vibration or light strike impacts.
- Bump Guards and Bollards – when a forklift strikes a pallet rack array, they most often contact the vertical posts at the leading edge or end corners. These members are not designed to withstand the force of a moving forklift, and often fail entirely with even a seemingly light strike. Install bump guards, rails, and bollards around all racking corners and exposed sides to protect them from rouge forklift strikes. For drive-in racking, consider using floor guide rails to keep forklifts aligned.
- High-Visibility Painting – use industrial-grade, highly visible, reflecting painting to mark out forklift and foot traffic lanes, rack end and corner posts, and any other surface that presents a bump point.
- Traffic Mirrors – install traffic mirrors to protect lifts and employees from each other around blind corners, at merging traffic lanes, and at dock doors (for use when backing out of trailers).
About InCord
InCord manufactures custom safety netting solutions and lifting and rigging products for a range of industries. Our woman-owned Colchester, CT manufacturing plant is an ISO-9001 certified facility, housing a team ready to design and fabricate a unique netting solution to fit your needs. InCord was founded in 1995 and is a Connecticut Top Workplace. To discuss an application, request a quote, or obtain technical guidance, please call us at (860) 537-1414, submit a request here, or email us at netting@incord.com.
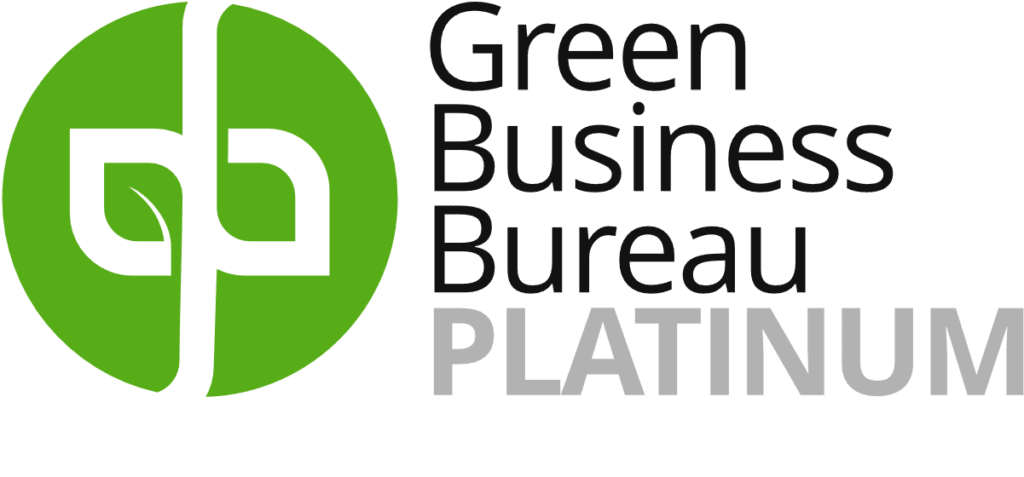
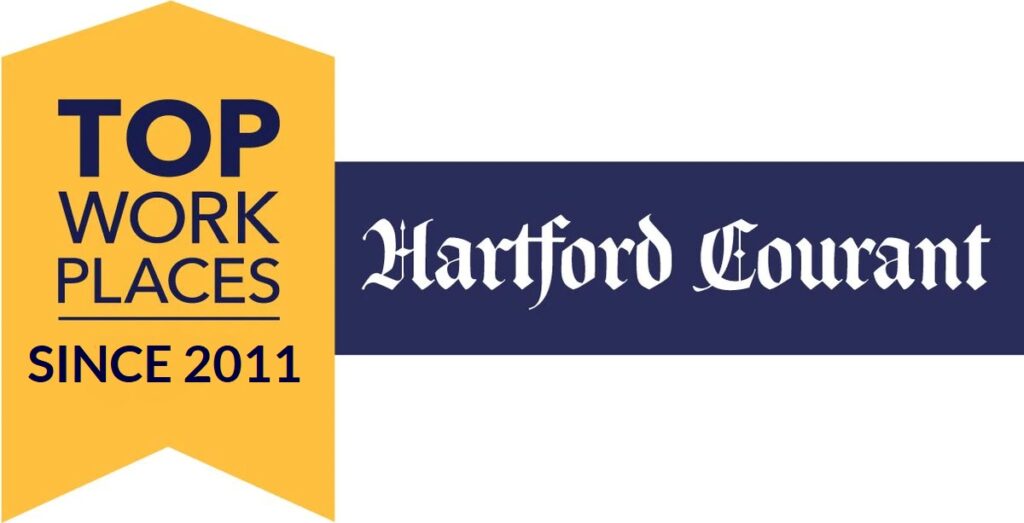
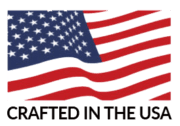